Design Philosophy
BeemCar uses modern, lightweight composite technology for the majority of its structural parts, based on the use of existing technology, proven in different applications across a broad range of industries, including the aerospace, rail, automotive and defence sectors – there is nothing new about the technology, only in the way that it has been brought together for this application. The design of BeemCar is driven by the key focus of passenger needs, guided by the following philosophy:
- KISS – Keep It Simple Stupid!
- Innovate and think outside of the box
- Provide a genuine alternative that will attract automobile users out of their vehicles
- Cater for all passenger types, irrespective of age or disability
- Ensure passengers are safe and secure during their journeys
- Minimise and manage risk
- Provide a reliable, low cost, fail safe system
- Be as environmentally friendly and green as possible
- Maintain an attitude of continuous improvement throughout the life of the system
- Work with, and bring benefits to local communities
BeemCar is not designed to replace other forms of public transport, but to be complementary and to work as part of an integrated transport system.
Design Specification
BeemCar is aimed at meeting the requirements of urban travellers, where there is the greatest need and the greatest potential through the development of linked networks, starting off with small routes and then linking them together. Most importantly, BeemCar is aimed at providing an effective contribution towards reducing congestion and the associated problems it causes, by offering an attractive and viable option to automobile users. Speed is restricted to 50 km/hr, as higher speed is unnecessary and leads to higher development, operating and maintenence costs. In addition, higher speed adds to the cost and size of stops, as longer ramps are needed for acceleration and decceleration. Intercity travel is a totally different requirement and is best left to services designed to meet this need.
Much effort has been put into the design of BeemCar’s pod to meet passenger requirements and make it an attractive alternative to automobile users. BeemCar has taken the approach that all pods need to be able to accommodate all types of passengers, as it will operate in a dense urban environment where it wouldn’t be practical or cost effective to operate different types of pods for different types of passenger; people with disabilities, including wheelchair and mobility scooter users, parents with buggies, cyclists and families going on holiday.
BeemCar’s passengers are accommodated in 4 forward-facing fixed seats, with a large floor area between for the wheelchairs and buggies. Just like in an automobile, the seats all face forwards, which is the arrangement that most aircraft and rail passengers prefer. It means that all passengers (even those in wheelchairs) will have a good view out of the windows without having to turn in their seats. In addition, it was also considered important that passengers could easily access pods, which is why BeemCar stops will mostly be at ground level, although there may be locations where a stop at the same level as the main beam traffic would be more suitable. For example, stops in shopping malls or large office complexes, where the stops can be inside the buildings.
Composite materials were chosen for the beam because of the significant advantages they offer; predominantly passenger comfort, but very importantly, low visual intrusion and low installation and through life costs. In addition, like aerospace, BeemCar has been designed to be ‘fail safe’, and with ‘lifed’ items – parts where failure would be catastrophic. For example, a fatigue failure of the linkage between pod and drive unit would result in the pod becoming detached and dropping 5m with the possibility of serious injury. These items deemed to be critical, would be tested to destruction and after applying a safety margin would be given a finite life to ensure they are replaced before they fail. Monitoring of usage would be automatic.
Although less efficient than rotary motors, LIMs were chosen to minimise the number of parts that would have to be carried around as dead weight, using energy unnecessarily. Less parts, particularly moving and complex parts, reduces maintenance costs and increases system reliability.
Maglev was considered but has not been used, as at 50 km/hr the advantages of Maglev are minimal and would be more costly than a simple set of very low friction free-wheeling support wheels. The difference in energy usage between that used by Maglev and the energy needed to overcome the friction of the wheels is negligible.
Why Suspended?
There are a number of major reasons for choosing a suspended system instead of a supported system using elevated guideways or rails:
- The running surfaces and systems needed to operate the pods are inside the hollow beam, protected from the weather, and from obstacles that would stop the system operating. For example, in stormy weather, there are no rails or tracks to become blocked, whereas in a traditional supported system, there would be a need for inspection and the clearance of debris
- Therefore, suspended provides higher reliability and lower maintenance costs
- The running surfaces are low friction and non-metallic, so there would be little, if any, ice build up
- No de-icing required, so reduced costs and all-weather operation
- The ability to tackle steep inclines that would be impossible in a supported system
- Enables ground level stops
- Provides a greater choice of route
- To provide the best possible comfort and experience for passengers:
- Panoramic views
- Spacious accommodation
- Pods will always remain horizontal, even when climbing inclines, whereas supported and multipoint suspended systems have to follow the gradient of the guideway or beam, which causes passengers to suffer the ‘roller-coaster’ effect when the pod transitions from one angle to another at the summit
- Safer and more secure
- Because the beam is at least 7m from the ground, access for animals, children and cable thieves, is prohibitive
- Because of the limited access, BeemCar is able to use mains power, with the cables and busbars hidden inside the beam
- Low visual intrusion, a major factor when it comes to community acceptance
- The beam is about a third the width of the pod compared to a supported system where the guideway width is usually greater than the vehicle width
- The beam is at least 2m higher than an elevated guideway, and therefore, further away from a viewer on the ground
- The smaller size beam compared to elevated guideway will cost less
- Installation is less disruptive and costs are lower
The H-Bahn at the University of Dortmund and Dusseldorf Airport, is an example of a suspended monorail, as is the Wuppertal Schwebebahn, which is a testament to the durability and longevity of suspended systems. It is the world’s oldest monorail in its 113th year of operation, proving the concept and with an unbeatable safety record for a public transport system.
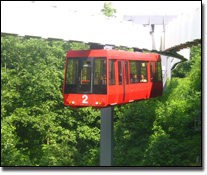
H-Bahn Monorail
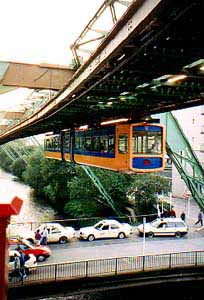
Wuppertal Schwebebahn